A complete asphalt paving estimate should cover five essential components. You’ll need detailed breakdowns of labor costs ($600/day for 4-person crews) and equipment rates ($1,200/day). Material specifications must include asphalt mix type and quantities (110 lbs per square yard). Site preparation requirements like grading and drainage solutions are vital. Project timelines should outline each phase with a 20% buffer. Don’t forget warranty terms and maintenance schedules – these details protect your investment. The deeper you investigate these components, the more confident you’ll be in your contractor selection.
Key Takeaways
- Labor and equipment costs should detail hourly rates for crew members, machinery rentals, and specific mobilization expenses for the project.
- Material specifications must outline asphalt mix type, required tonnage, base materials, and surface thickness measurements with exact quantities.
- Site preparation requirements should specify grading work, drainage solutions, soil compaction standards, and necessary surface preparation steps.
- Project timeline needs to include all phases from permitting through installation, with clear completion dates and weather contingency plans.
- Warranty terms and maintenance schedule should detail coverage period, recommended maintenance intervals, and specific conditions for warranty validity.
Labor and Equipment Breakdown
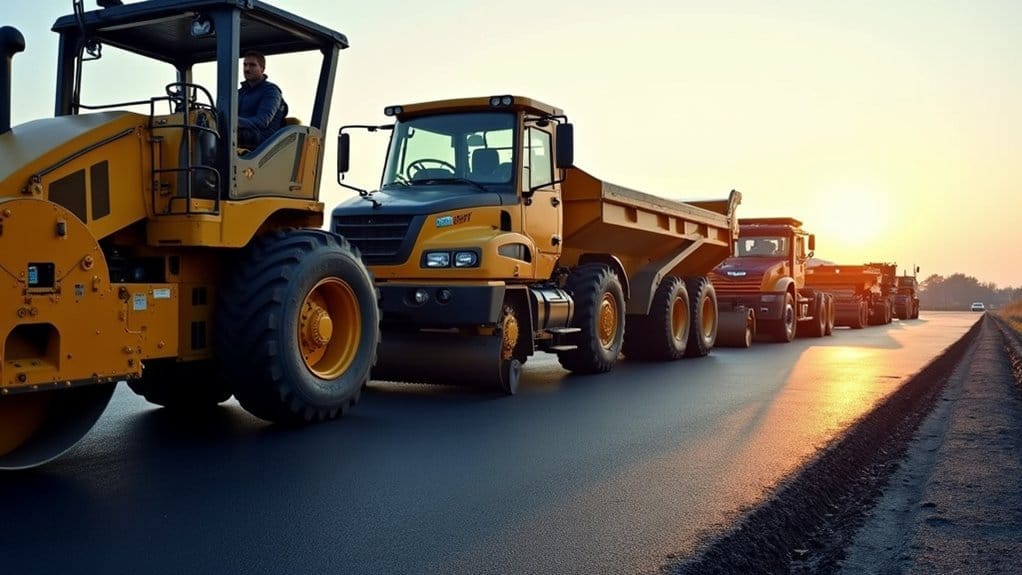
Three key elements make up the labor and equipment costs for asphalt paving.
First, your labor costs include skilled operators, general laborers, and a site supervisor. You’ll need people who know what they’re doing! Each crew member’s hourly rate and expected project duration will impact your total estimate.
Equipment types are your second major consideration.
You’ll need:
- Pavers ($150-300/hour)
- Rollers ($75-125/hour)
- Dump trucks ($85-150/hour)
- Support vehicles ($45-65/hour)
Finally, don’t forget mobilization expenses. Getting all that heavy equipment to your job site isn’t cheap! You’ll pay for transport trucks and fuel costs.
Let’s break down a typical project:
✓ 4-person crew: $600/day
✓ Essential equipment: $1,200/day
✓ Mobilization: $400-800 per project
Additionally, understanding the importance of regular maintenance can help you plan for future costs and extend the lifespan of your pavement.
These numbers help you understand where your money’s going!
Material Quality and Quantity Details
When planning your asphalt project, material costs will make up 40-60% of your total budget!
Your estimate should clearly outline key material specifications:
- Asphalt mix type (hot vs. warm)
- Grade of materials (commercial or residential)
- Surface thickness (typically 2-4 inches)
- Base layer requirements
The quantity calculations must be crystal clear too:
- Total square footage
- Tonnage requirements (1 inch depth = 110 lbs per square yard)
- Additional materials needed (tack coat, aggregate base)
You’ll want to see exact numbers! A quality estimate breaks down materials like this:
- Commercial-grade hot mix: 85 tons
- 3/4″ aggregate base: 125 tons
- Tack coat: 55 gallons
Don’t accept vague material descriptions. Get specific details that match your project requirements! Additionally, working with a reliable paving company ensures that you receive accurate estimates and high-quality materials tailored to your needs.
Site Preparation Requirements
Proper site preparation can make or break your entire asphalt project!
You’ll need expert site grading to create the perfect foundation. Don’t skip this critical step! Your contractor should assess the existing ground conditions and determine the ideal slope for water runoff.
Key Site Prep Requirements:
- Remove all vegetation and debris
- Compact the soil properly (95% density minimum!)
- Install reliable drainage solutions
- Level the subgrade accurately
- Test soil stability
Watch out for these red flags:
- Standing water areas
- Soft or unstable soil spots
- Improper grading angles
- Missing erosion controls
Your contractor should outline specific drainage solutions in the estimate. This includes catch basins, French drains, or surface channels.
Great drainage prevents future pavement failure and extends your asphalt’s lifespan by years! Additionally, ensure your contractor has a strong local reputation to instill client trust in their services.
Project Timeline and Scheduling
Planning your asphalt project‘s timeline requires careful coordination between multiple teams!
Let’s break down your project phases:
- Site assessment: 1-2 days
- Permits and approvals: 2-4 weeks
- Surface preparation: 3-5 days
- Asphalt installation: 1-3 days
- Curing time: 24-72 hours
Watch out for these scheduling challenges:
- Weather delays (rain or extreme temperatures)
- Equipment availability
- Material delivery timing
- Crew scheduling conflicts
- Local regulations and restrictions
Pro tip: Build in a 20% time buffer! You’ll want flexibility for unexpected issues.
The best times for paving are spring and fall. Summer heat can affect installation quality. Winter conditions aren’t ideal for proper curing.
Remember: Good planning prevents project delays. Your contractor should provide a detailed timeline with clear milestones. Additionally, consider the importance of customer satisfaction as a key aspect of project success.
Warranty and Maintenance Specifications
Standard Warranty Coverage
Your estimate should include clear details about warranty terms. Most reputable contractors offer 2-5 years of coverage for workmanship and materials.
Make sure you understand what’s covered and what’s not!
Essential Maintenance Details
A proper maintenance schedule will extend your asphalt’s life considerably.
Your estimate should outline:
- Annual sealcoating recommendations
- Crack filling intervals (typically every 2-3 years)
- Weight restrictions for vehicles
- Snow removal guidelines
- Drainage maintenance requirements
Regular sealcoating can extend asphalt life by 30-50% compared to unsealed surfaces, making it an essential part of your maintenance plan.
Documentation Requirements
Keep records of all maintenance performed. This helps protect your warranty coverage!
Many contractors require proof of regular maintenance to honor their warranty terms. Ask for a detailed maintenance checklist with your estimate.
Additional Cost Considerations and Add-ons
Beyond the base estimate, several key add-ons can impact your final paving costs!
Let’s investigate what you need to watch for.
Common Add-ons to Evaluate:
- Grading and site preparation
- Additional material costs for deeper base layers
- Drainage solutions and water management
- Line striping and parking lot markings
- Traffic control during construction
Watch Out for These Too:
- Removal of existing pavement
- Unexpected site issues like soft soil spots
- Equipment mobilization fees
- Permits and inspections
- Special coating or sealant applications
Pro Tip: Always ask your contractor about potential add-ons upfront!
In addition to these considerations, keep in mind that regular maintenance services can help prevent future issues and save costs in the long run.
It’s better to budget for these extras now than face surprises later.
Most quality contractors will walk you through each possible addition during the estimation process. They’ll help you understand which ones are essential for your specific project.
Conclusion
When it comes to asphalt paving estimates, you’re now armed to the teeth with essential knowledge! Don’t settle for vague quotes or unclear terms. Make sure your estimate includes every detail we’ve covered – from labor costs to warranties. You’ll save time, money, and headaches by getting it right the first time. Take charge and demand complete transparency. Your perfect pavement project is just a detailed estimate away!