When considering the cost of commercial sealcoating, factors like repairs extent, sealer type, and area size influence the overall expenses. The square footage directly impacts the total cost as prices are determined per square foot. Larger areas require more materials and labor due to the significant quantity of sealant needed. Crack repairs are essential for maintaining asphalt integrity and durability. The location where the work is done can also affect costs based on labor rates and material availability. Using high-quality materials is vital for long-lasting protection against various elements. For a thorough understanding of commercial sealcoating costs, consider these influencing factors.
Key Takeaways
- Factors include repairs, sealer type, coats, and surface prep.
- Cost influenced by area size, materials, and labor.
- Crack repairs crucial for structural integrity and longevity.
- Location impacts labor rates and material availability.
- High-quality materials offer lasting protection and value.
Factors Influencing Commercial Sealcoating Cost
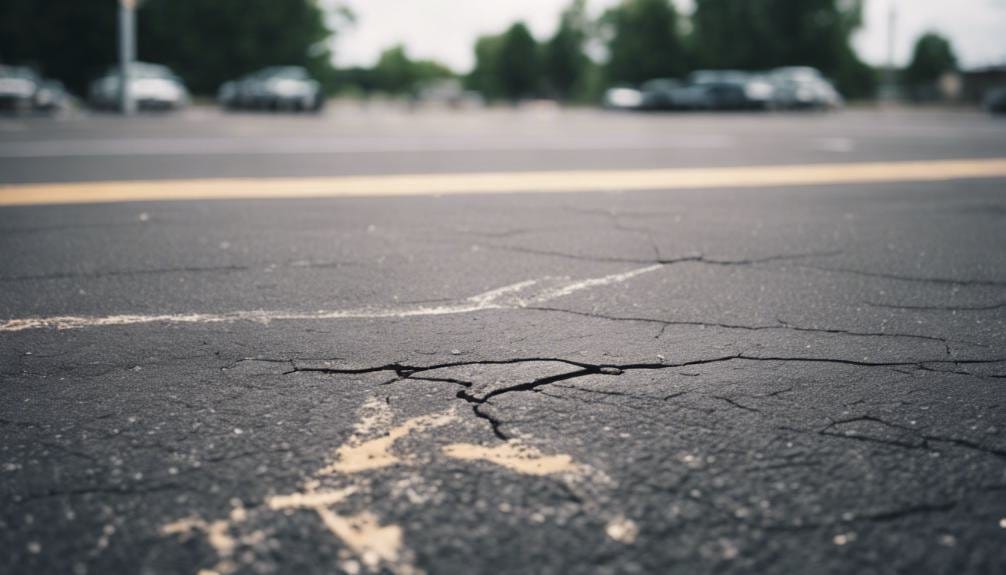
Factors that greatly impact the cost of commercial sealcoating include the extent of necessary repairs, the type of sealer utilized, and the number of coats required for best protection. Proper surface preparation is vital before sealcoating a commercial parking lot. Inadequate preparation can lead to premature failure of the sealcoat, resulting in higher overall costs. Repairing cracks and making sure the asphalt surface is clean and free of debris are essential steps that contribute to the final sealcoating cost.
Choosing the right type of sealer is another critical factor. Different sealers have varying costs and performance characteristics. Higher quality sealers may come at a higher price but provide better protection and longevity, ultimately impacting the overall cost of maintenance over time.
Labor fees also play a significant role in determining the sealcoating cost for commercial parking lots. Skilled labor is required for proper application, which guarantees a durable finish. Factors such as labor efficiency and experience level can impact the final expenses.
Size of the Area to Be Sealed
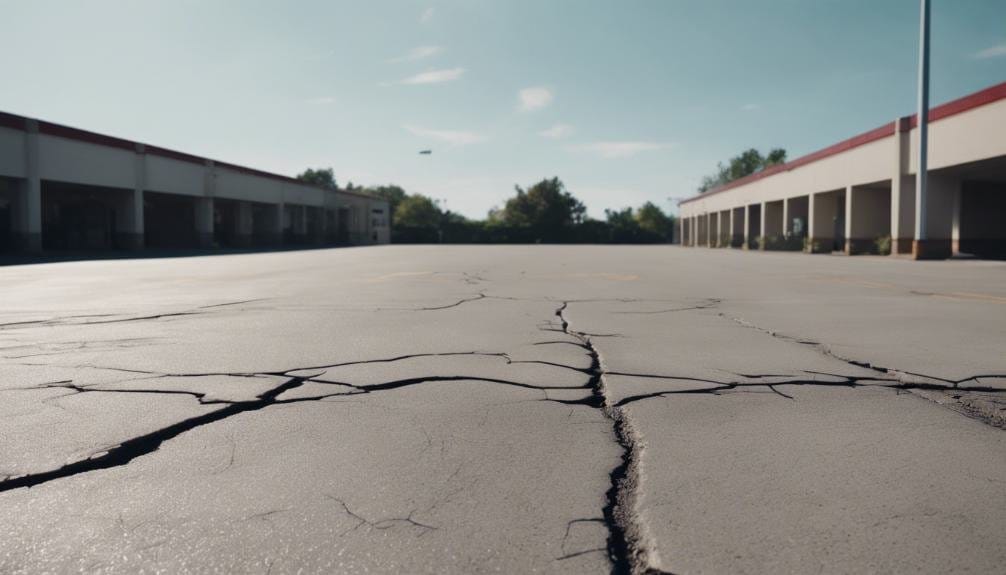
The size of the area designated for sealcoating directly influences the overall cost of commercial sealcoating projects. When calculating the cost, the square footage of the lot or parking area plays an important role. Sealcoating prices are commonly determined per square foot, where larger areas like asphalt parking lots entail higher costs due to the increased materials and labor required.
The quantity of sealant needed is directly proportional to the size of the area to be sealed, impacting the final pricing significantly. Hence, understanding the square footage of the space needing sealcoating is essential for precise cost estimation and effective budget planning for commercial properties.
As the size of the area to be sealed increases, so does the overall cost of the sealcoating project, making it imperative to accurately measure and assess the dimensions of the lot or parking space before proceeding with the sealcoating process.
Need for Crack Repairs
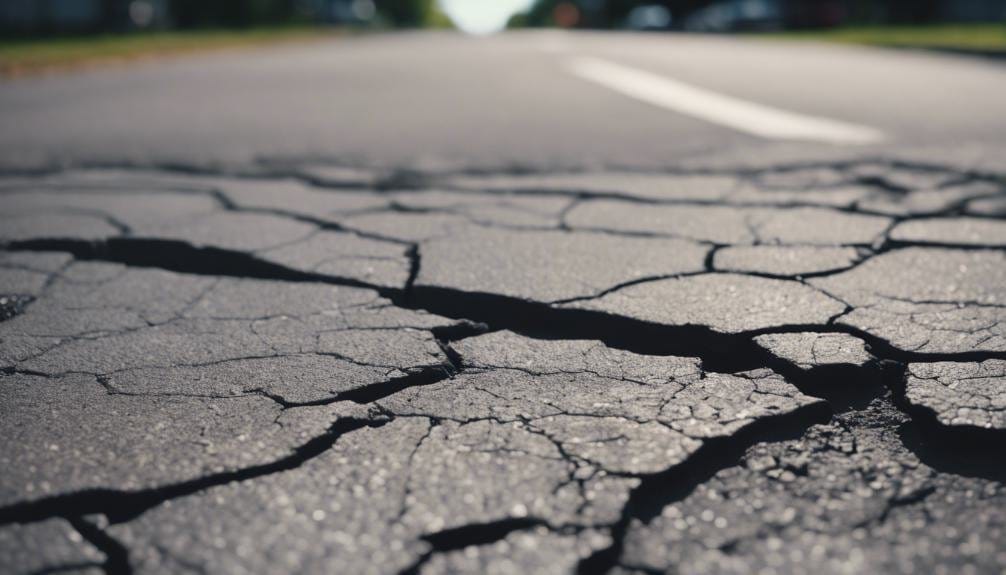
Address the importance of crack repairs before sealcoating by ensuring the asphalt’s structural integrity and preventing water intrusion. Proper crack repairs are essential in maintaining the asphalt surface. Neglecting crack repairs can lead to accelerated pavement deterioration and diminish the effectiveness of the sealcoating application.
When cracks are left unattended, water can infiltrate the asphalt surface, causing erosion, potholes, and structural issues over time. Effective crack repairs play a significant role in preserving the pavement’s integrity, extending its lifespan, and reducing the likelihood of costly repairs in the future.
Professional sealcoating contractors typically include crack repair services as part of their preparation process to guarantee a durable and long-lasting sealcoat application. By addressing crack repairs before sealcoating, you can enhance the overall quality and longevity of your pavement while protecting it from water intrusion and associated damages.
Partnering with experienced professionals ensures that your asphalt surface receives proper maintenance and care.
Location Impact on Cost
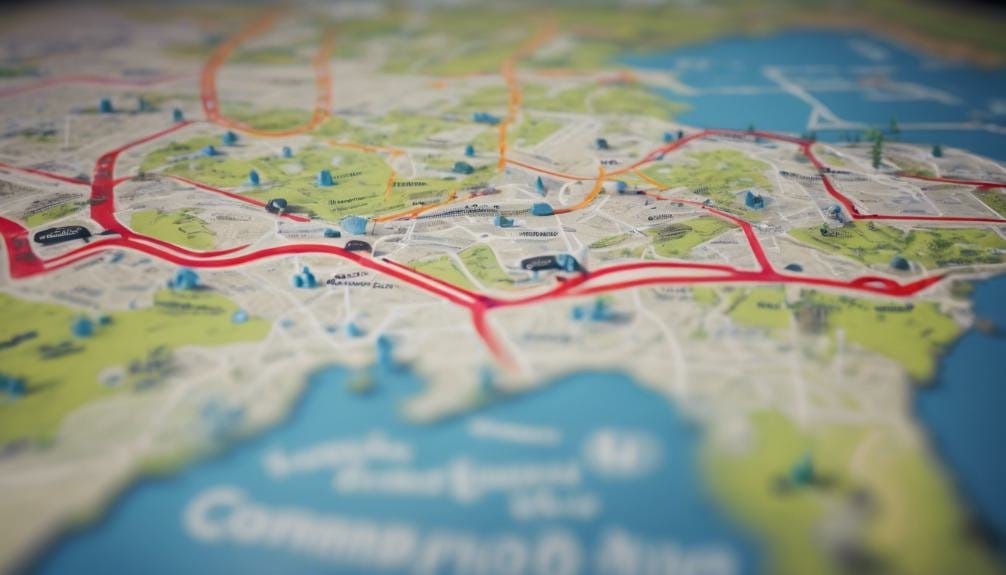
Location greatly impacts the cost of commercial sealcoating due to varying labor rates, material availability, and local market competition. When considering seal coating for your commercial property, it’s essential to recognize the significant influence of location on overall expenses. Here are some key points to understand this impact:
- Labor Rates: Different regions have distinct labor costs, affecting the total price of sealcoating projects. Urban areas often have higher labor rates compared to rural locations, leading to increased overall expenses.
- Material Availability: The accessibility of sealcoating materials can vary depending on the location. Limited availability or transportation challenges can result in higher material costs.
- Local Market Competition: Areas with more sealcoating companies competing for projects may offer competitive pricing, whereas regions with fewer providers could have higher costs due to limited options.
Considering these factors can help you anticipate and manage the expenses associated with commercial sealcoating in your specific location.
Quality of Materials Used
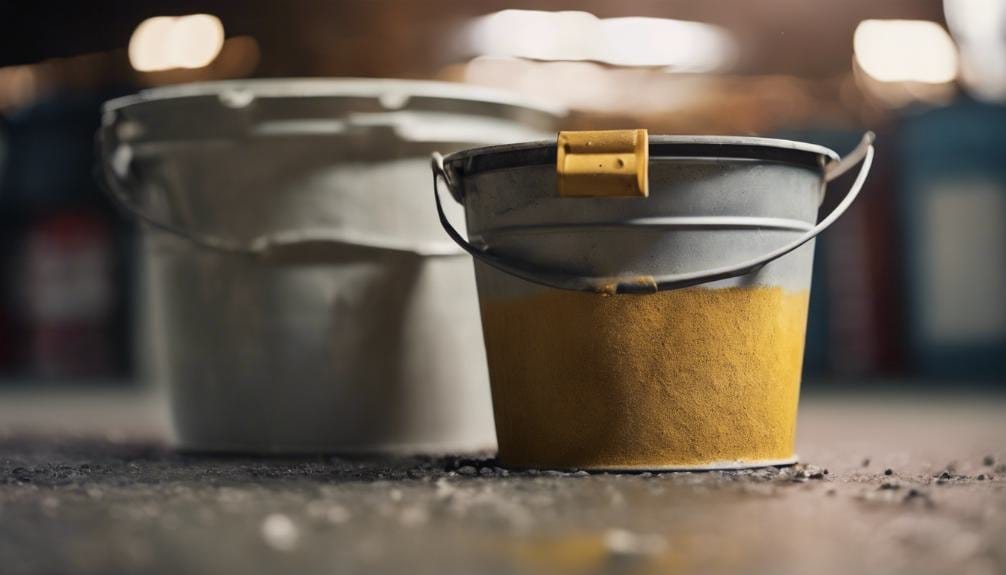
Taking into consideration the influence of geographical factors, such as labor rates and material availability, on commercial sealcoating costs, the quality of materials used becomes a crucial aspect to guarantee long-lasting protection for your surfaces.
High-quality sealcoating materials play an essential role in enhancing the durability and longevity of your commercial surfaces. Opting for premium materials may involve a higher initial cost, but in the long term, it can lead to cost savings by reducing the frequency of resealing.
Quality materials offer superior protection against various elements like UV rays, oil, weathering, and heavy traffic, thereby ensuring the longevity of the sealcoating. The durability of the sealcoating largely depends on the type and grade of materials utilized during application.
DIY Sealcoating Cost Comparison
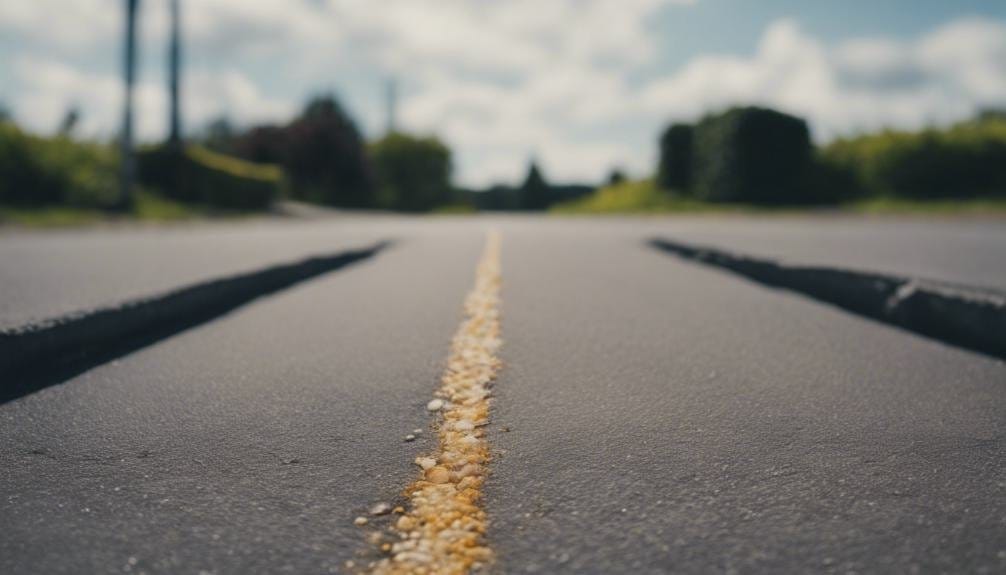
Investing in DIY sealcoating can offer a cost-effective solution for small areas, with costs ranging from $0.15 to $0.25 per square foot. When comparing the cost of DIY sealcoating to professional sealcoating, it becomes evident that the former is more economical for smaller projects. Here are some key points to take into account in the DIY sealcoating cost comparison:
- The average cost to DIY sealcoat a 600 square foot space falls between $90 and $150, depending on the materials utilized.
- Time and effort required for DIY sealcoating should be factored in, as it may not be feasible for larger areas.
- Factors influencing DIY sealcoating costs involve labor, sealer type, number of coats required, and the surface size.
While DIY sealcoating can be a budget-friendly option for minor areas, opting for professional sealcoating is advisable for larger spaces to consider proper application and durable outcomes.
Importance of Proper Crack Repair
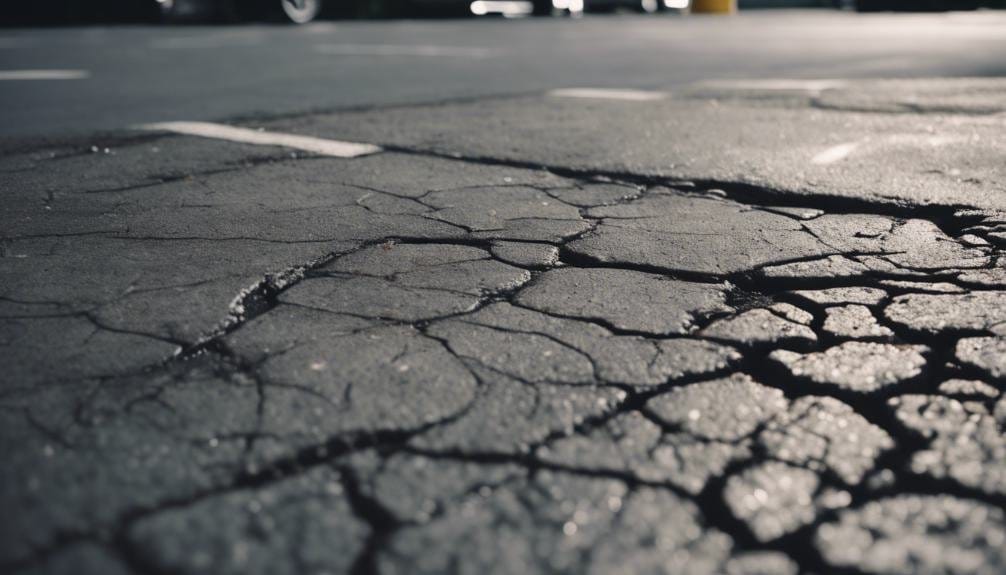
Proper crack repair in commercial sealcoating is essential for maintaining the structural integrity of asphalt surfaces and preventing water-induced damage. Commercial sealcoating involves sealing asphalt pavements to protect them from the elements and traffic wear. Without proper crack repair, water can infiltrate the pavement, leading to accelerated pavement deterioration. Professional crack repair techniques, such as cleaning, filling, and sealing cracks, are vital to prevent moisture penetration and preserve the pavement’s integrity.
Effective crack repair guarantees a smooth surface for the sealcoat application, maximizing its protective benefits and extending the lifespan of the asphalt parking lot. Neglecting crack repair can result in costly repairs or premature resurfacing due to advanced pavement deterioration. Investing in professional crack repair as part of regular commercial sealcoating maintenance can greatly reduce long-term repair expenses and enhance the overall durability of the pavement. Prioritizing proper crack repair is a cost-effective strategy to prevent extensive damage and maintain the quality of asphalt surfaces.
Significance of High-Quality Materials
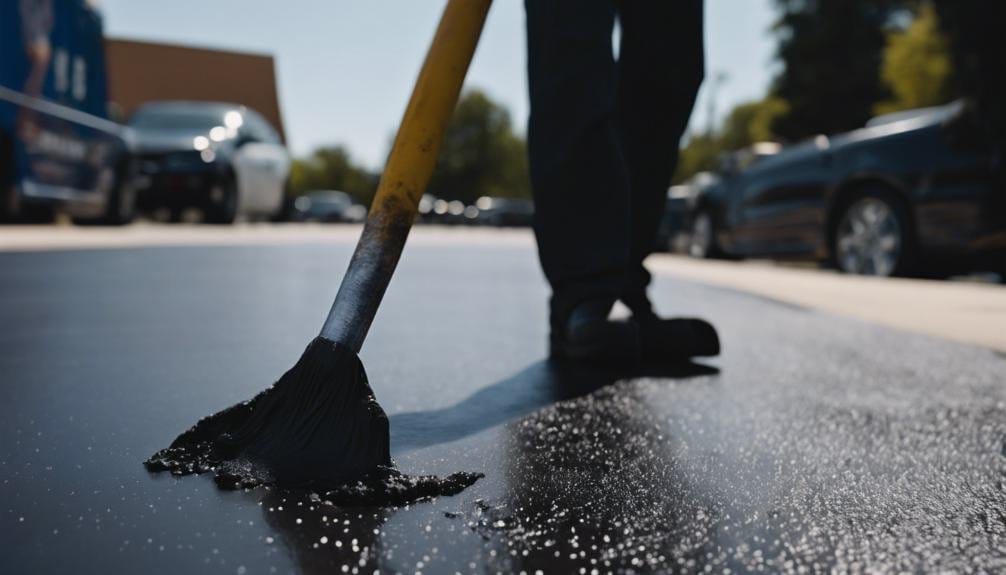
Using high-quality materials for sealcoating is vital for guaranteeing maximum protection and longevity of asphalt surfaces. When it comes to sealcoating your asphalt driveway or commercial properties, opting for premium materials can make a significant difference in the long-term maintenance and durability. Here are three key reasons why investing in high-quality materials is essential:
- Long-Lasting Protection: High-quality sealcoating materials offer superior protection against UV rays, gasoline, and contaminants, extending the lifespan of the asphalt surface and reducing the risk of premature deterioration.
- Cost-Effective Maintenance: Quality materials result in fewer cracks, chips, and potholes, minimizing the need for expensive repairs or early repaving. This cost-effective approach can save you money over time by reducing maintenance expenses.
- Enhanced Property Value: By using top-grade sealants, you not only secure the longevity of your asphalt but also enhance the overall aesthetics of your property. This can add value to commercial properties and maintain a professional appearance for years to come.
Thorough Preparation for Sealcoating
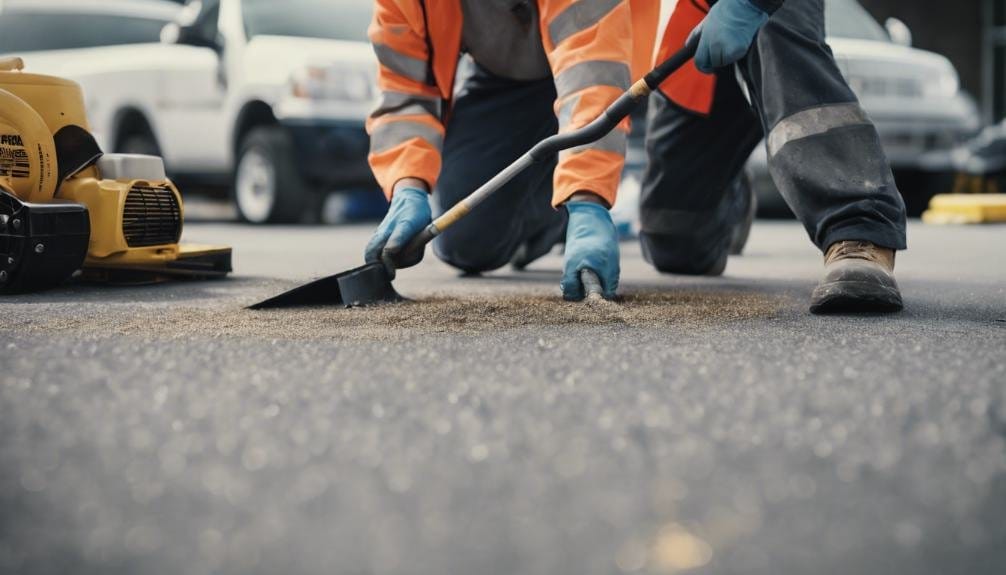
To ensure the effectiveness of your commercial sealcoating project, meticulous surface preparation is essential, starting with thorough cleaning to eliminate dirt, debris, and oil spots. Adequate surface preparation is vital to achieving a durable and long-lasting sealcoat.
Power washing the surface helps remove ingrained dirt and prepares the asphalt for sealing. Additionally, filling cracks and addressing any potholes before sealcoating is essential for ensuring a smooth and even finish.
Thorough preparation not only improves the adhesion of the sealcoat but also enhances the overall appearance of the asphalt surface. By taking the time to properly prepare the area, you’re investing in the longevity and effectiveness of your commercial sealcoating.
Longevity and Effectiveness of Sealcoating
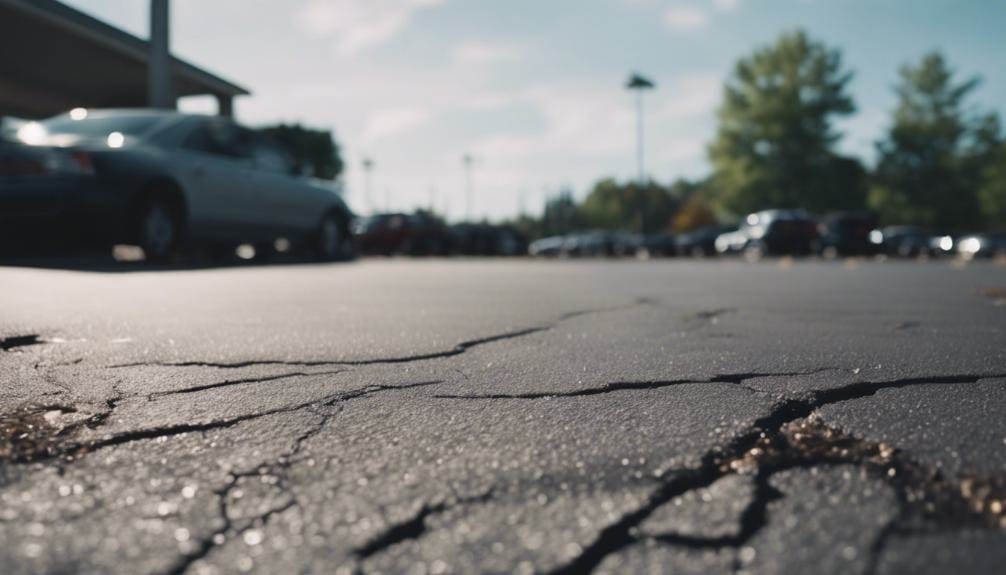
For optimal durability and cost-effectiveness, guaranteeing the longevity and effectiveness of sealcoating is essential in preserving asphalt surfaces for decades. Sealcoating can extend the life of asphalt by up to 36 years, saving on costly repaving expenses. It prevents cracks, chips, and potholes, maintaining the appearance and durability of the surface.
Commercial sealcoating costs range from $36.9 to $61.5 per car in parking lots, depending on size and condition. For larger areas like basketball courts, the cost can be $705 to $1175, ensuring long-term protection and savings. Regular sealcoating is a cost-effective way to preserve asphalt surfaces for over 30 years, avoiding premature deterioration.
Regular sealcoating helps in safeguarding asphalt from UV rays, preventing premature aging. Asphalt emulsion-based sealcoating provides a smooth and durable surface, enhancing the longevity of the asphalt. Hiring professional sealcoating contractors guarantees proper application techniques, maximizing the effectiveness of the sealcoating.
Conclusion
When considering the cost of commercial sealcoating, it’s important to remember that the size of the area, need for crack repairs, location impact, and quality of materials all play a role in determining the final price.
Proper crack repair and high-quality materials are essential for the longevity and effectiveness of sealcoating. In fact, studies have shown that using high-quality materials can increase the lifespan of sealcoating by up to 50%.
Remember, investing in quality now can save you money in the long run.